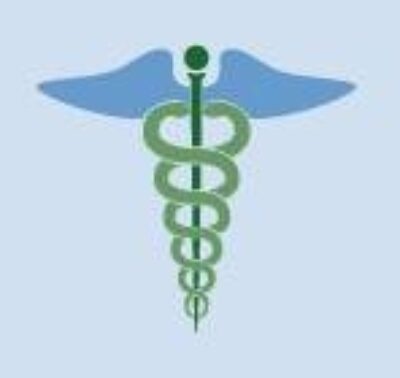
HICprevent
This award-winning blog supplements the articles in Hospital Infection Control & Prevention.
Check it don't infect it: Joint Commission creates checklist for endoscope reprocessing areas
March 18th, 2015
With infections related to contaminated endoscopes a recurrent problem in health care, The Joint Commission has created the following checklist for assessing reprocessing areas to better ensure patient safety:
Environmental tour checklist for endoscope reprocessing areas
Physical space: Is the area sized appropriately in relation to the volume of equipment processed?
Do staff put on personal protective equipment (PPE) before entering the area?
Are staff wearing suitable PPE?
Is there sufficient work space?
Are cleaning supplies, storage areas, and other critical items clearly labeled?
Is there an appropriate hand washing station?
Is there an appropriate eyewash station?
Are “dirty” areas physically separated from “clean” ones?
Are there suitable storage areas for cleaned endoscopes? On visual inspection, do these areas look clean, free of debris and dry?
If a cabinet serves as storage, does the cabinet have doors?
Are endoscope storage containers dry and located off the ground”?
What is the route from the processor to the cabinet? (The route should not cross through the soiled processing area.)
Ventilation:
Is there negative air pressure to surrounding areas?
Are air exchange rates and filtration efficiencies appropriate? Are there a minimum of 10 exchanges per hour, with at least two being with fresh, outside air?
Is exhaust vented directly outside?
Documentation and training:
Are staff aware of the number of endoscopes in the department?
Does staff know how frequently these are maintained and how that maintenance occurs?
When staff members are questioned, can they show where evidence-based practices and guidelines are located?
When staff are asked about their training, does it appear they were trained using the guidelines?
Are staff given periodic refresher training?